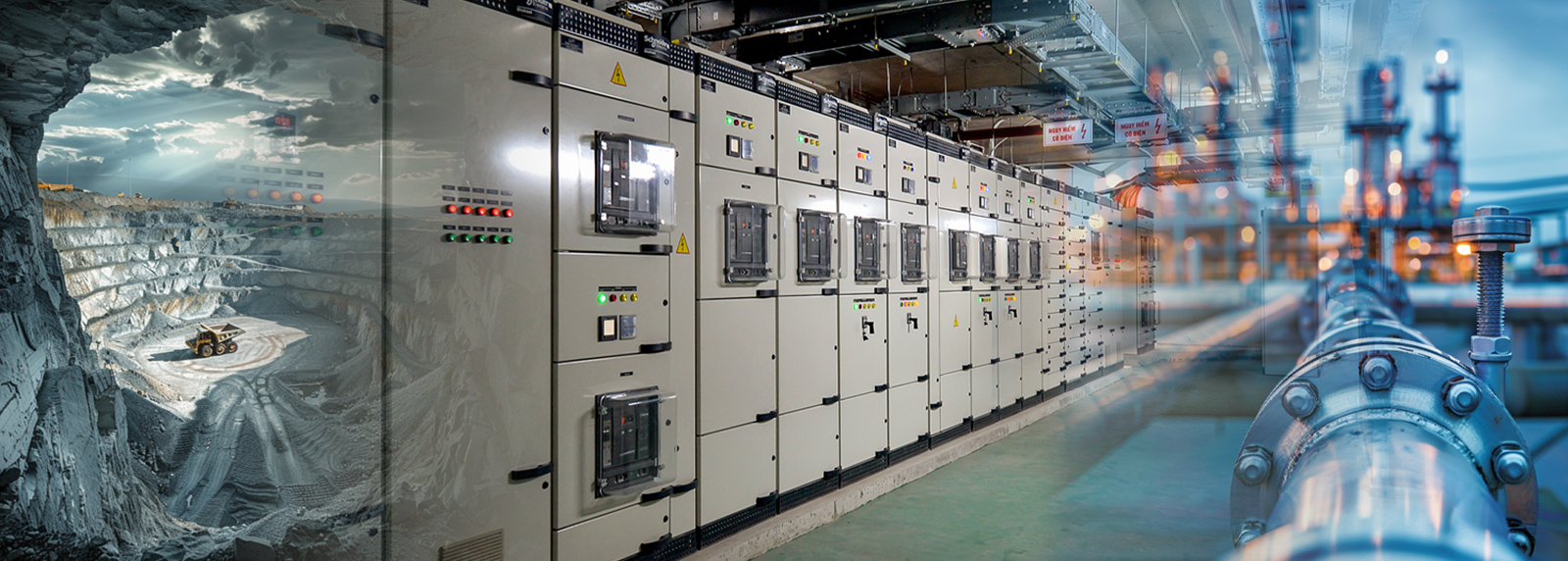
Medium Voltage Variable Frequency Drives (MV Drives)
Can-Technologies is committed to deliver a reliable integration of MV Drives and improve operational efficiency.
Medium Voltage VFDs are advanced electronic devices designed to control the speed of medium voltage electric motors, typically ranging from 2.3kV to 15kV for up to 2400 kVA.
Next generation of variable speed drives, designed to deliver IIoT benefits with built-in intelligence to gather data and share information.
Can-Technologies dedicated MV Drive team is committed to work with you and choose the right technology for your project. Our proposed solution will be tailored to your specific needs. Our expertise in power control and automation, coupled with dedication to customer satisfaction, we ensure seamless integration, reliable performance, and long-term support for your MV Drive upgrade projects.
Altivar – the smart, connected Medium Voltage Variable Speed Drive
The latest modular high quality MV Drives allow a wide range of power from 700 HP to 6,500 HP @ 4,160V, 3-phase. By managing the frequency and voltage supplied to the motor, these new drives (i.e Altivar ATV1260 & ATV6000) offer precise control over motor speed, enabling optimization of energy usage and enhancing process efficiency.
Common Issues and Challenges for MV Drives
Choosing, installing and integrating MV Drives can be very challenging. Here is highlight of common issues and challenges around MV Drives:
- Reliability and Maintenance: MV drives are critical components in industrial processes, and downtime can result in significant losses. Designing MV Drive with the latest and cost-effective technology is crucial for minimizing unplanned downtime and optimizing asset utilization. Challenge: Designing for reliability and ease of maintenance to minimize downtime.
- Integration with Existing Systems Upstream/Downstream: MV drives often need to integrate with existing control systems and infrastructure. Ensuring compatibility and seamless integration while minimizing disruption to operations can be challenging. – Challenge for Upstream: Integration has multiple challenges such as Communication Protocols between different components involved, Hardware Compatibility with the existing system, bidirectional data exchange between a MV drive and SWGR, Transformer and grounding system, Data Synchronization, interfaces and interlock between components. – Challenge for Downstream: Motor Compatibility, Motor Protection and Safety, Field Harmonics Mitigation, Voltage and Frequency Compatibility, Adapting to Load Variations, Voltage Transients and Surge Protection.
- High Voltage Handling: MV drives operate at voltages typically ranging from 1 kV to 15 kV require specialized components. – Challenge: Ensuring safe operation and insulation at high voltages.
- Heat Dissipation: MV drives handle large amounts of power, leading to significant heat generation. – Challenge: Managing heat generation effectively to prevent overheating and cooling system provisions for the drive and installation location.
- Efficiency: Optimizing switching topologies and control algorithms to minimize power losses and improve efficiency. Challenge: Achieving high efficiency across various operating conditions.
- Harmonics and EMI: MV drives can generate harmonics and electromagnetic interference (EMI). Mitigating these effects often require additional filtering and shielding measures such as Implementing passive or active filtering techniques. Challenge: Mitigating harmonics and electromagnetic interference (EMI) to maintain power quality.
- Mechanical Design: MV drives are often large, heavy and hard to provide a safe mechanical protection. Challenge: Designing robust mechanical structures including their support to fit in the existing/new layout to support the weight, dive cooling system and withstand environmental stresses including provisions for moving to installation location.
- Protection and Safety: It is essential for MV drives to have comprehensive protection features for safeguarding against overcurrent, overvoltage, short circuits, grounding system configuration, ride through, power outage, unplanned disconnection and other faults or manual operation. Challenge: Implementing comprehensive protection features to safeguard against faults and ensure operator safety and compliancy with safety standards and regulations.
- Complex Control Algorithms: MV drives employ sophisticated control algorithms. Implementing vector control algorithms or model predictive control (MPC) techniques are complicated and hard to achieve a precise control. Challenge: Developing sophisticated control algorithms to regulate voltage, frequency, and torque accurately.
- Startup and Commissioning: Conducting thorough testing and tuning of the VFD parameters (e.g., acceleration/deceleration rates, voltage/frequency control and forbidden speeds) to achieve desired motor speed, torque control and performance. Challenge: Properly commissioning the VFD and existing motor to ensure smooth startup, stable torque, safe operation, and optimal performance in permitted speeds.
- Training and Documentation: Developing comprehensive operation manuals, maintenance procedures, and training programs tailored to the specific requirements of the VFD and motor integration.
- Cost Considerations: MV drives can be expensive due to their high-power ratings and specialized components. Balancing performance requirements with cost considerations is essential. Challenge: Selecting cost-effective components and optimizing design parameters to achieve desired performance within budgetary constraints.
Applications and Industries
Discover the Versatility of Medium Voltage VFDs:
- Steel Industry: Enhance the efficiency of steel manufacturing processes including rolling mills, blast furnaces, and electric arc furnaces, reducing energy consumption and improving overall production output.
- Water and Wastewater: Enhance pump efficiency in water treatment plants and distribution systems, ensuring reliable and cost-effective operation.
- Mining: Improve conveyor belt performance and ventilation systems, maximizing productivity while minimizing energy costs and equipment wear.
- Oil and Gas: Optimize pumping systems and compressor operations, reducing energy consumption and enhancing production efficiency in upstream and downstream processes.
- Manufacturing: Fine-tune motor speeds in manufacturing processes such as extrusion, machining, and material handling, improving process control and product quality.
Experience the Future of Power Control with Medium Voltage VFDs from Can-Technologies. Contact us today to learn more about our solutions and how we can empower your industry.